Pre-Construction technology allows contractors to work collaboratively with other contractors and vendors to design a project with all the appropriate physical and mechanical attributes within the same digital space. Architects, general contractors, and various sub-contractors specializing in multiple disciplines such as piping, plumbing, HVAC, structural steel, electrical, and fire protection work together to create a design that is a safe, efficient, and effective solution for the customer. These tools, processes, and software allow all contractors working on the project to identify concerns or collisions ahead of time in a digital environment and prevent issues in the field where it gets to be much more costly to experience delays or overlapping contractor schedules. By having the mechanical systems modeled, the contractors can better plan the prefabrication and coordination on the job site before the project even starts.
TERMS TO KNOW
How does it work? Before we explain the system, let’s first define the terms.
CAD: Computer Assisted Design- “the design tools”
Design and documentation tool that can be done in either 2D or 3D. This is a technological software tool with a variety of different software available (Soldiworks, Inventor, AutoCad, Revit etc.).
MEP: Mechanical, Electrical, Plumbing-“the discipline”
This captures the three main disciplines other than the building itself required in all commercial and industrial buildings in one acronym.
BIM: Building Information Modeling – “the model”
Process of collaboration that is facilitated by digital technology. The key difference between a BIM and a 3D CAD model is that a BIM file is much more information-rich and includes details of performance characteristics, specifications, and other non-physical data embedded in a shared 3D digital model for the project.
VDC: Virtual Design and Construction-“the process”
Method of planning and managing a BIM project collaboratively. Think of VDC as how we perform the work from design through installation by using technology, tools, and resources to collaborate and process the information efficiently within the model.
THE PROCESS
Our VDC team uses CAD/MEP software and tools to create the digital design of our systems within the 3D Building Information Model. From the model we then export layout points and installation drawings for the field, fabrication drawings, and cut files to the CNC cutting equipment. By modeling the installation using digital representations of the mechanical systems, components, and equipment we process the work more accurately and efficiently and eliminate many manual processes. This technology along with tools such as the RTS (Robotic Total Station) for laying out supports, equipment and penetrations from the model in the field, and using 3D scanning for capturing onsite data, streamline the construction process and mitigate risks.
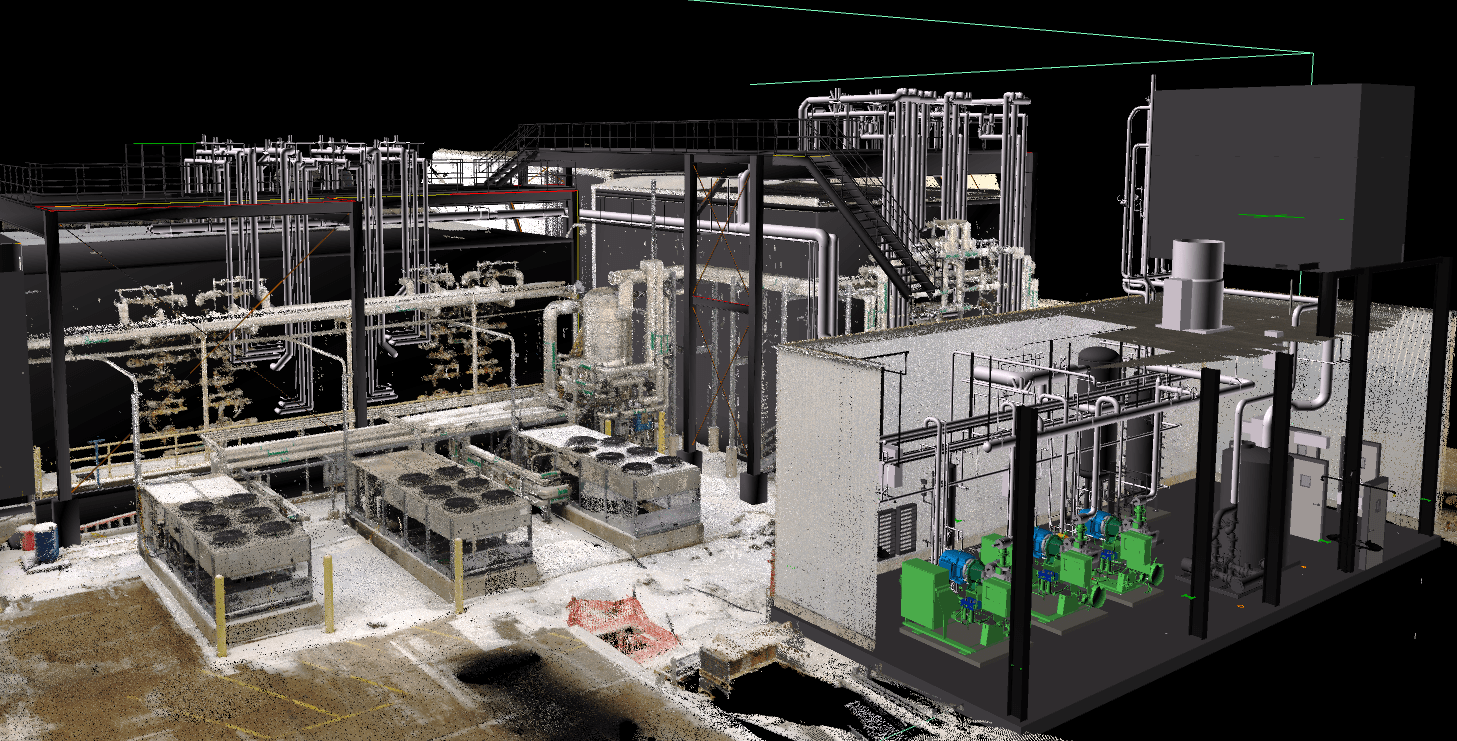
There is a vast amount of software available today for BIM technology and it is rapidly improving and growing. Because there is no one specific software that works perfectly for every trade discipline or accounts for all components and details (yet), we have implemented a LEAN approach which applies the optimal amount of software to fit the application and minimizes steps to create the design, fabricate the components, and install the mechanical systems with the least amount of processing time and hand-offs. This approach minimizes the risk of issues as the project is underway and maximizes the quality of the solution for customers.
Want to learn more? Check out this 3D project spotlight!