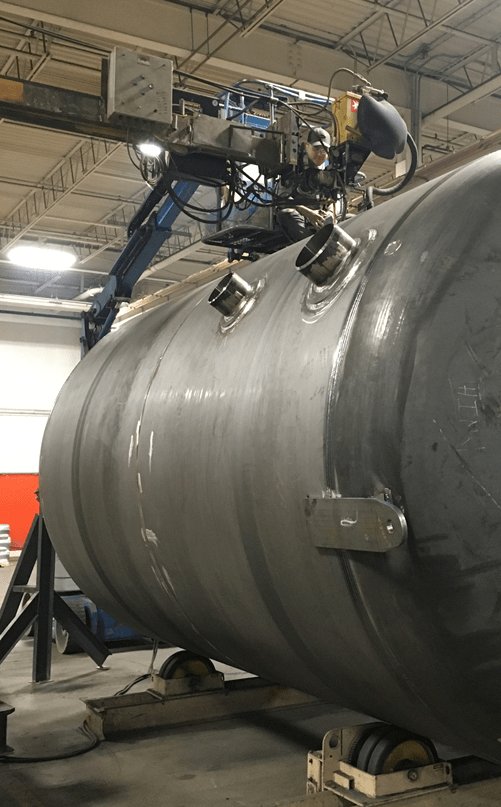
In the Industrial Refrigeration Handbook (1998), Professor Wilbert Stoecker offered general thoughts on the sizing of refrigeration vessels. In his comprehensive text, he consolidated his opinion as, “Never scrimp on the size of the vessel.”
Today, application requirements and changes in design philosophy have increased the focus on refrigerant charge reduction and thereby vessel size reduction. However, due to the size of refrigerated facilities, the proven reliability of liquid recirculation systems, the enhanced protection provided for compressors, the ability to handle refrigerant surges, and the inherent adaptability for future expansions, many refrigeration vessels used today are still very large.
Thermatech, a Bassett Mechanical company, has developed specialized processes and techniques to build such large vessels, often 10 or 12 feet in diameter, to serve the refrigeration market.
APPLICATION OF CODES AND REQUIREMENTS
To begin, for use in the United States, the vessel must be designed to satisfy application, ASME Code, and IIAR Standard requirements. As a pressure-containing vessel holding large quantities of ammonia, the design requires the review and stamping by one of our Professional Engineers, for safety and suitability of purpose.
To meet application and regulatory requirements, large pressure vessels have extra heavy wall thicknesses which we begin to prepare as steel plate. Using computer-aided design and processes, our CNC plasma table utilizes a fully articulating plasma head to cut the material and to pre-cut openings for pipe connections in the plate, accounting for the dimensional changes as the flat steel plate will be rolled into a cylindrical shape.
VESSEL FORMATION
As a next step, the rolling of flat plate (can be 1” thick or more) into a large diameter vessel shell needs to be performed on a large rolling/forming machine with provisions to accommodate and support the substantive weight of the material.
As the circular shell of the vessel is formed, the mating ends are tack welded together in preparation for the heavy deposition of material in the longitudinal seam weld.
In addition to the seam weld, in very large vessels, circular sections are joined together to extend the vessel’s length through a circumferential welding process. With the welder positioned above the vessel, the vessel is rotated with the root weld applied by hand and subsequent layers applied through a precisely controlled, continuous sub-arc welding process.
A complex, heavy, and cumbersome welded assembly of vessel heads, lugs, and connections is completed to prepare the vessel for hydrostatic testing.
NON-DESTRUCTIVE TESTING
Additional non-destructive testing services provided can include partial or full x-ray of welds to document full weld penetration and joint stability.
Ammonia refrigeration requirements often introduce another complexity to vessel construction. Concern for stress corrosion cracking (a metallurgical risk) introduces requirements to heat treat pressure vessel heads and leads to customers requesting post-fabrication heat treatment of the entire vessel. This necessitated the development of a skilled supply chain, with very large capacity heat-treating furnaces.
“Never scrimp on the size of the vessel.” -Professor Wilbert Stoecker
Surface preparation for field installation can vary based on whether insulation is to be applied with additional requirements for corrosion protection or due to customer paint specifications. Larger vessels require special consideration for the safe application of the required finishes at heights.
RESPONSIBLE SOLUTIONS
Larger refrigeration vessels require specialized skills and processes, and additional safety measures, and we are glad to apply these on behalf of our customers.
Applying our refrigeration knowledge ensures that our vessels meet the expectations of our customers and the safety requirements of their intended use.
Learn more about our vessel capabilities!